Current Practice in New Homes
Almost all of the 64 homes tested for envelope leakage as part of the Field Study were in compliance with the 7 ACH50 (Air Changes per Hour at 50 pascals pressurization) leakage rate required by the 2009 IECC. However, more than a third were above 5 ACH50 and almost 90% were above 3 ACH50.
Energy Code Requirements
The 2015 IECC requires that all homes be tested for envelope leakage. In climate zone 2 the envelope leakage rate must be 5 Air Changes per Hour or less, tested at 50 Pascals (ACH50). In climate zones 3 and 4 the ACH50 must be 3 or less. The previous TX state energy code, the 2009 IECC/IRC, allowed either a visual inspection or testing and required a leakage rate of 7 ACH50 or less.
Bringing all new homes into compliance with the 2015 IECC requirements for envelope leakage will save Texas homeowners $4,656,869 every year.
Guidelines for Envelope Sealing
Know Where The Air Barrier Is and How It Will Be Sealed
The 2015 IECC/IRC require that the building thermal envelope and air sealing details be shown on the construction documents. A good example is when specifying a house wrap, make sure to specify seam and flashing tapes that are compatible with that house wrap and provide details for seams, window and other areas that need flashing. This is not just a code requirement but also excellent practice.
Know It’s Sealed Before Testing
Finding out a home does not pass the envelope leakage test after the walls are sealed and all the finishes are complete can be an expensive and time consuming mistake. The energy code provides a very comprehensive set of criteria for air barriers and insulation installation in Table R402.4.1.1 (N1102.4.1.1 in the IRC). If the air barrier criteria in this table are met, a home will pass the envelope leakage test. Make sure the air barrier has been thoroughly inspected and any gaps, seams and penetrations are well sealed before any insulation or drywall is installed.
Know Who Is Responsible For the Air Barrier
Framers will be responsible for installing the initial air barrier. The foundation of the air barrier is proper framing, blocking and installation of the rigid air barrier. If the air barrier strategy includes a house wrap the framer will also need to install it and make sure the seams are properly taped and details around openings like windows and doors are properly flashed and sealed.
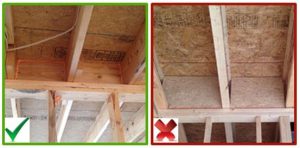
Blocking between garage and conditioned space.
Electricians, plumbers and other trades have to be responsible for sealing any penetrations they make in the air barrier. If these trades leave their penetrations to be sealed by the insulation contractor there will almost certainly be openings that do not get sealed because the insulation contractor didn’t know where to look.

Sealing electrical box in ceiling.
Photos: Appalachian State University Energy Program
Insulation contractors are your last line of defense in air sealing. Before beginning the insulation the contractor must perform an pre-insulation inspection and make sure that all gaps, seams, joints and penetrations are sealed and that the air barrier is continuous from ridge to foundation and is completely sealed, with no penetrations, gaps, cracks or seams left unsealed.
Testing
Use independent, third party testing contractors who are Resnet Certified Home Energy Rater or Field Inspector, or Building Performance Institute Certified Infiltration and Duct Leakage Professional or Building Analyst, or other certification approved by the local Building Official.